Insights
Cleaning and the effects of retained cleaning water in tank coatings
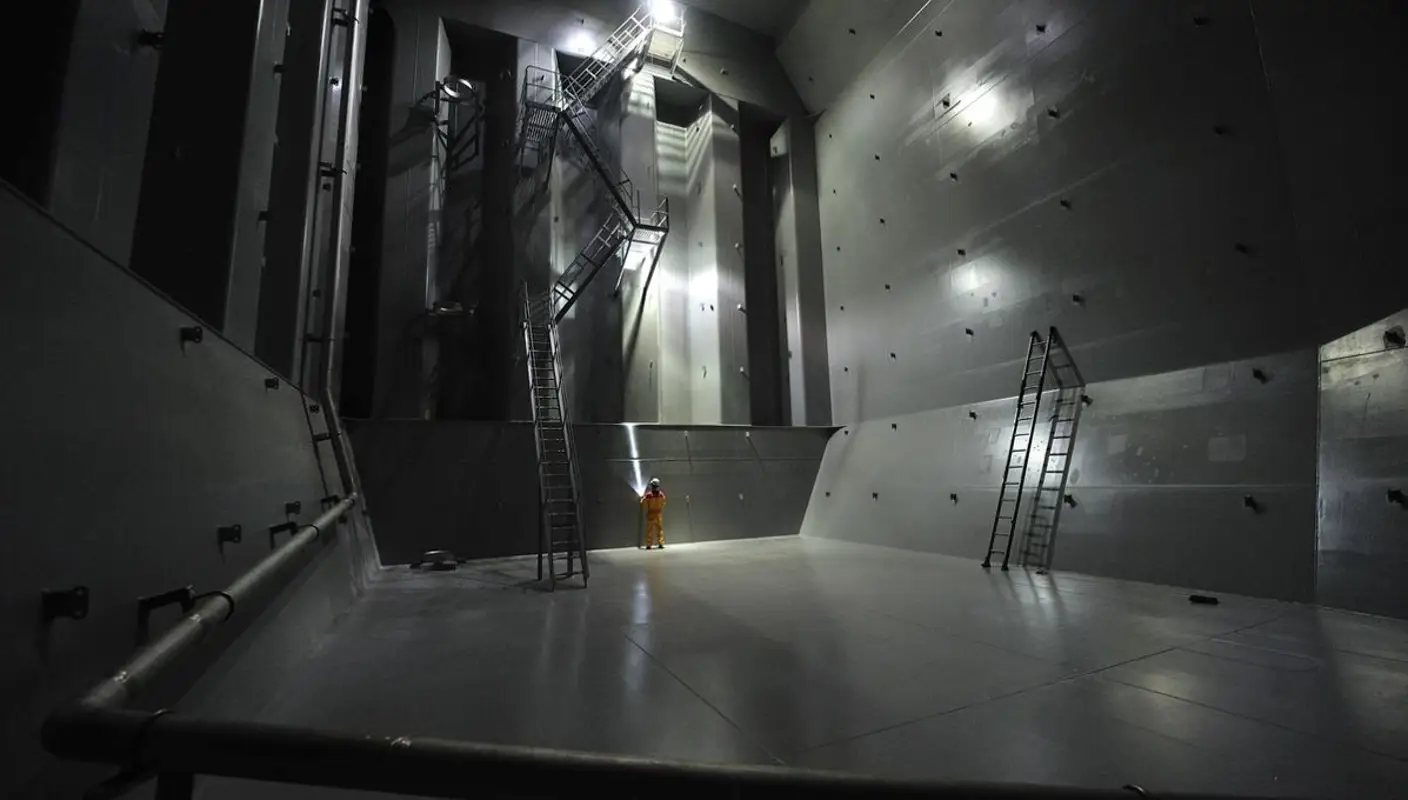
september 06, 2017
Water retained in cargo tank coatings after cleaning could result in corrosion and cargo contamination. Recent research tests show different epoxy tank coatings have varying absorption and desorption qualities.
Experimental procedures
In the never ending battle against corrosion, ships need to be protected inside as well as outside. Protecting cargo tanks against corrosion is particularly important as they represent integral parts of the structure of the ship.
A range of coatings have been developed to protect different types of cargo tanks against corrosion and their cargo against contamination. Which coating system is used will depend on the ship type, trade and cargoes carried. Operators have individual needs and requirements, also with regards to cleaning tanks.
Explaining the background for the research, Gard Reian, researcher at Jotun Performance Coatings Research & Development, said: “As water is used to clean cargo tanks between different cargoes shipped, a cargo tank coating is generally exposed to water more frequently than to any single cargo. Water retained in the coating after cleaning could potentially result in problems; one possible issue could be water contamination of the cargo, another is the failure of the coating itself due to the formation of corrosive reaction products (hydrolysis). To shed more light on this, we conducted tests to study the amount, and rate of, water absorption of four commercially available epoxy tank coatings and, more importantly, how long ventilation time the absorbed water needs to fully leave the coating.”
Commercial tank coatings tested
Jotun tested four different epoxy tank coatings and these are shown in Table 1, together with information on the technology base and curing regime.
Reian explains: “The coatings were applied onto Mylar® polyester films for easy removal of free films. The coatings were applied using a fixed frame applicator, with the aim to get a dry film thickness in line with the respective product’s technical data sheet (TDS). After application, the coatings were cured as per their respective TDS and/or application guidelines. The free coating films were then cut using a scalpel in squares of approximately 2 x 2 inches, and each square was weighed before immersion.
“During the absorption period the coating squares were immersed in fresh (tap) water or sea water (1), in closed containers at ambient temperature (1). The samples were removed at intervals for weighing. All excess surface liquid was removed with a dry paper towel before each weighing. Weighing was performed using an analytical balance to ~0.1 mg. Also, during the desorption period the coating was left to ventilate on the bench under ambient conditions (21 °C - 23 °C, 20 - 40 % relative humidity) and weighed periodically. The absorption-desorption experiment was run over three cycles to study the accumulated effects of water uptake” added Reian.
[1] Artificial sea water was made per recipe given in ASTM D 1141.

Expanding on the process and definitions, Reian describes sorption as the combined processes of adsorption and absorption (1). Adsorption is the physical adherence or bonding of ions and molecules onto the surface of another phase. Absorption is the incorporation of a substance in one state into another of a different state. “For the sake of this article, we will assume that the migratory process is purely absorptional and all the molecules contributing to weight gain are incorporated in the free volume of the coating film.”
He continued, “Desorption is a phenomenon whereby a substance is released from or through a volume. The process is the opposite of sorption (that is, either adsorption and absorption). This occurs in a system being in the state of sorption equilibrium between the bulk phase and an absorbing volume (coating film). When the concentration (or pressure) of substance in the bulk phase is lowered, some or all of the sorbed substance returns to the bulk state”.
Reian pointed out that the absorption and diffusion of water in polymeric materials such as epoxy systems is related to the free volume (2,3) and the polymer-water affinity (3,4) The amount of free volume depends on the molecular packing and is affected by both the crosslink density (and therefore the extent of curing) and physical aging (4). The polymer-water affinity is significantly influenced by the presence of hydrogen-bonding sites within the polymer (6). Water can sometimes be absorbed without causing swelling; when this happens, it is suggested that it remains unbound to the polymer and is effectively accommodated within the free volume (4).
Varying results
Figure 1 and Figure 2 show that for all coatings, and for all cycles, absorption stabilizes quite fast (reaches equilibrium) within a few days. The absorbed amount of water is considerably higher for coating B and D. “This indicates that these coatings have a higher molecular affinity for water and/or a higher free volume,” said Reian and added, “Previous absorption testing (not published) indicates a predominance of the first effect (higher affinity towards water) for these two products.”
The figures also reveal that for all coatings, the desorption rate is fast and an equilibrium is reached within 24 hours of perfect ventilation. [1] For coating A and C all the absorbed water has left the coating within 24 hours of ventilation, as can be seen by the graphs coming to equilibrium around the horizontal axis. For coating B and D, there seems to be a considerable retention of water. Even after 10 days of perfect ventilation there is still water left in the paint film, and it even seems to accumulate from the second to the third test cycle noted Reian.
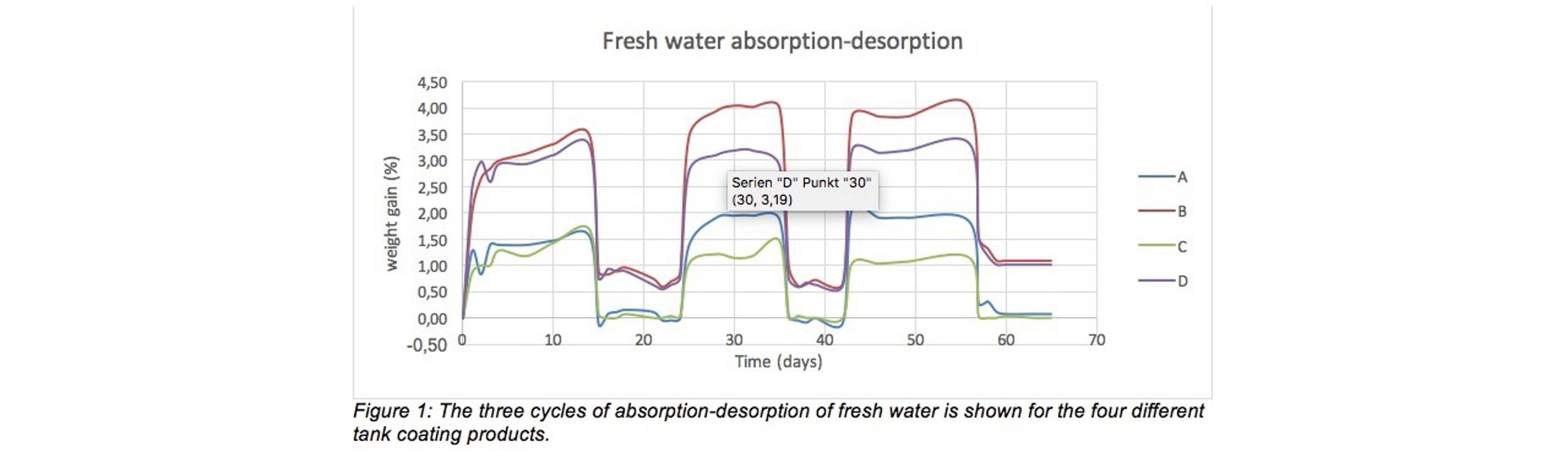
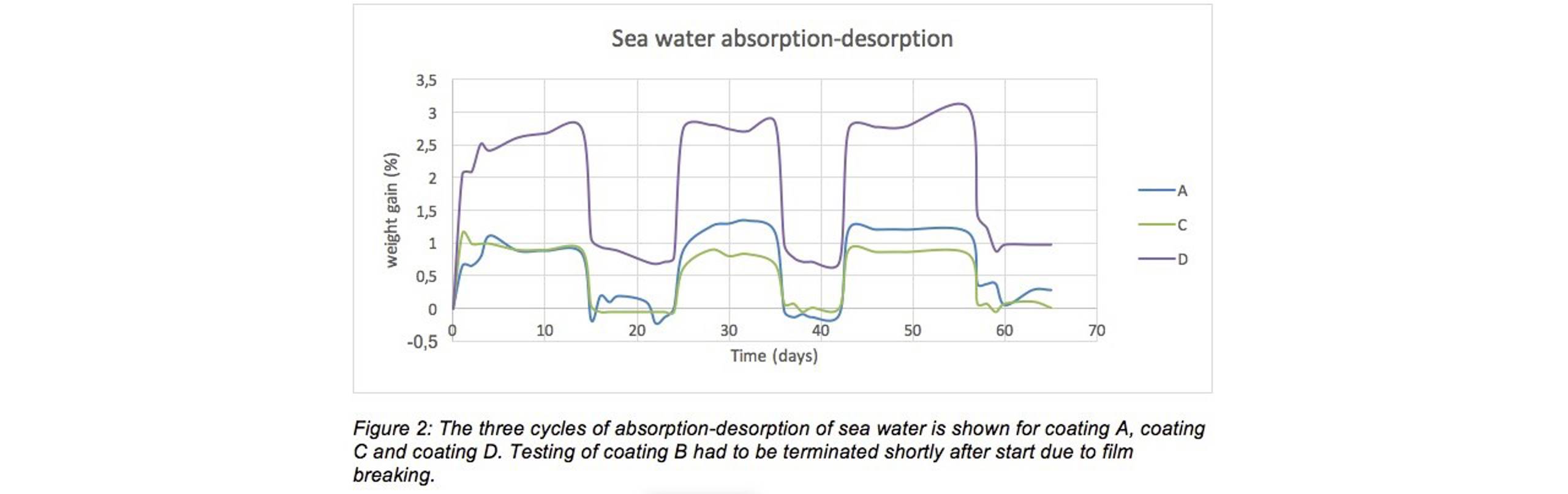
Figure 1 and Figure 2 show that for all coatings, and for all cycles, absorption stabilizes quite fast (reaches equilibrium) within a few days. The absorbed amount of water is considerably higher for coating B and D. “This indicates that these coatings have a higher molecular affinity for water and/or a higher free volume,” said Reian and added, “Previous absorption testing (not published) indicates a predominance of the first effect (higher affinity towards water) for these two products.”
The figures also reveal that for all coatings, the desorption rate is fast and an equilibrium is reached within 24 hours of perfect ventilation (2). For coating A and C all the absorbed water has left the coating within 24 hours of ventilation, as can be seen by the graphs coming to equilibrium around the horizontal axis. For coating B and D, there seems to be a considerable retention of water. Even after 10 days of perfect ventilation there is still water left in the paint film, and it even seems to accumulate from the second to the third test cycle noted Reian.
**
[2] The free films of coating in this experiment were left to ventilate in a, relative to area, infinite volume of air. The desorption rate will depend on the access to "fresh" air and so the results might be different for a more poorly ventilated storage tank.
Can adversely affect coating lifetime and performance
“It is difficult to predict the exact effect of water retention in a tank coating, but one has to wonder if it will affect coating lifetime and performance, especially if the coating is exposed to a water sensitive or an easily hydrolysable cargo,” said Reian.
Regarding the difference between fresh water (Figure 1) and sea water (Figure 2), all coatings absorb a higher amount of fresh water. This confirms fresh water penetrates more easily into the coatings film, when compared to sea water.
Considerable differences
“Our tests on the four commercially available epoxy tank coatings, each based on a slightly different binder technology, reveals that there are considerable differences between the various coatings when it comes to water absorption and subsequent desorption.
“The pure epoxy and novolac epoxy coating absorbed less water overall and desorbed faster and more completely than the coatings based on novolac-RDGE or epoxy-silicon. The latter two coatings retained a lot of water, even after as much as ten days of perfect ventilation,” said Reian and concluded, “As to the difference between fresh water and sea water, the coatings generally absorbed a higher amount of the fresh water than they did sea water.
Literature
- Sax, N.I.; Lewis, R.J.L Sr. Hawly`s Condensed Chemical Dictionary, Eleventh Edition, Van Nostrand Reinhold: New York, 1987.
- Duda, J. L.; Zielinski, J. M. In Diffusion in Polymers; Neogi, P., Ed.; Marcel Dekker: New York, 1968.
- Van der Wel, G. K.; Adan, O. C. G. Prog. Org. Coat., 1999, 37, 1.
- Van Landingham, M. R.; Eduljee, R. F.; Gillespie, J. W. J. Appl.Polym. Sci., 1999, 71, 787.
- Struik, L. C. E. Physical Aging in Amorphous Polymers and Other Materials; Elsevier: Amsterdam, 1978.
- Adamson, M. J. J. Mater. Sci., 1980, 15, 1736.