Insights
Energy transition: why maintaining steel integrity has become critical in ensuring safety, efficiency in operations and reduced emissions
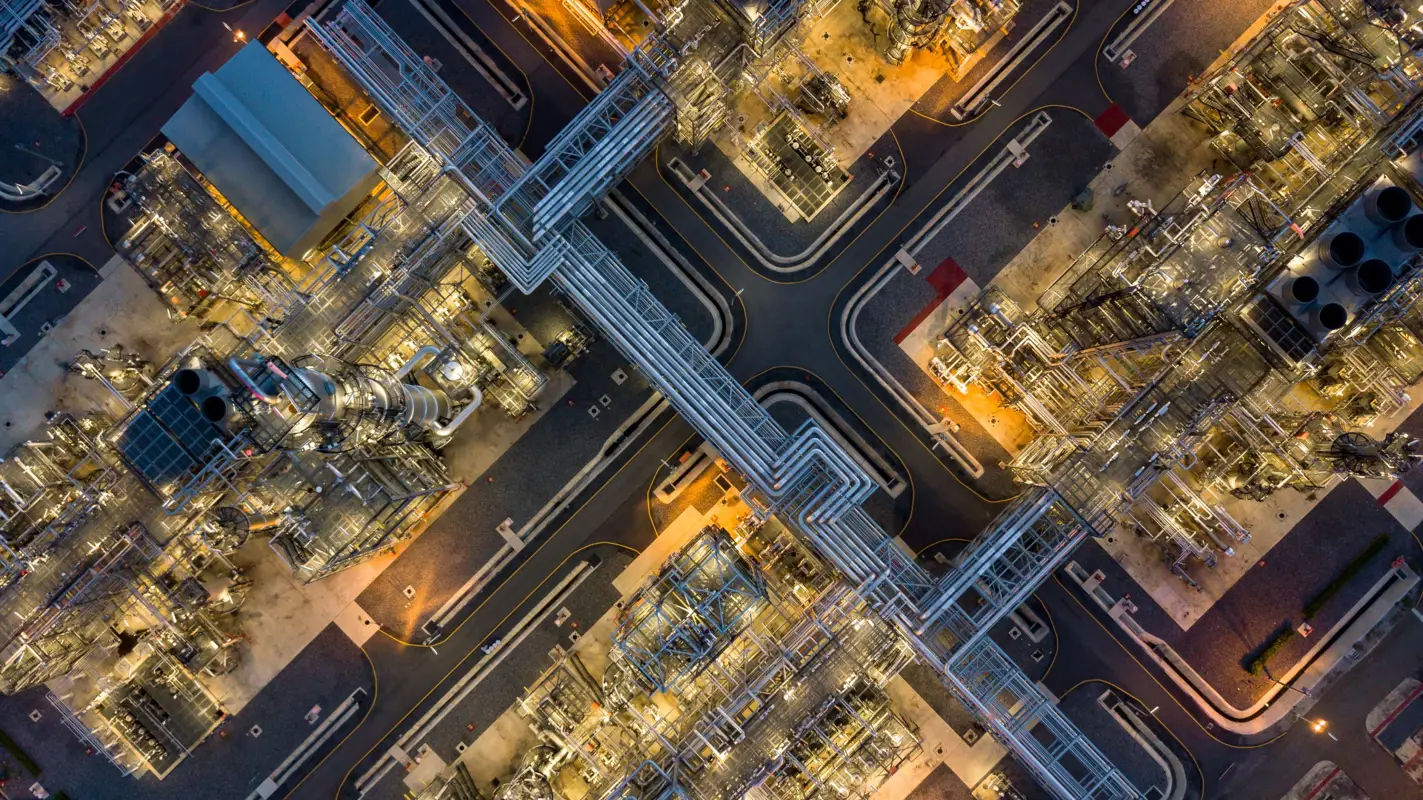
Nisan 12, 2024
Corrosion, chemicals, heat and fire can cause major headaches for the energy sector which relies heavily on the integrity of steel components. In the first of a series of articles around the importance of maintaining steel integrity we examine the extent of the problem and identify the main areas of concern for onshore energy facilities.
Globally, demand for energy is set on an accelerating upward trend that shows little sign of a slow down any time soon. There is much talk of an energy transition taking place but for several reasons the pace is slower than anticipated or hoped for. Renewable projects, for example, are not increasing at a fast enough pace to match demand because rising costs for raw materials and services are hitting the return on investment.
Also, as the 2050 target for reaching net zero draws ever closer, the global contribution of fossil fuels is not decreasing at a rate even close to what it should be to hit the target. That means a more responsible approach for fossil fuels use is needed which has implications in many areas. Especially important is ensuring that a core component in energy production and distribution facilities – steel – is protected sufficiently to ensure safety and efficiency of essential energy infrastructure.
Fossil fuels an essential part of energy needs
Data on energy sources can vary according to who is reporting but the differences are quite small. In the 30 years from 1990 to 2020, the share of energy supplied by fossil fuels has fallen from around 90% to about 85% with the rest being provided by nuclear, hydropower and mostly recently renewables.
This represents a drop in terms of overall share for fossil fuels, but such has been the growth in energy demand and production, that Enerdata suggests power supplied by fossil fuels has moved from around 8,500 mtoe (million tonnes oil equivalent) in 1990 to around 14,500 mtoe in 2020 – a 70% increase.
By contrast, in 2022 the International Energy Agency (IEA) reported that renewable energy supply from solar, wind, hydro, geothermal and ocean rose by close to 8%, meaning that the share of these technologies in total global energy supply increased by close to 0.4 percentage points, reaching 5.5%.
It is therefore quite clear that as global demand for energy continues to rise fossil fuel asset owners seek to increase production at existing facilities and to invest in new facilities to keep pace.
Pressure on asset owners
There is however something of a dilemma for those asset owners. Whilst there is an obvious commercial case for continued investment, the energy transition would seek to draw a line under the use of fossil fuels and to encourage development of cleaner alternatives. This puts pressure on asset owners to consider what future legislation and levies on their products might mean in terms of productive lifetime.
Simultaneously, they also have to adapt to geopolitical events. Sanctions on products from states such as Russia, Iran and Venezuela and others have meant that some assets are underused while facilities in other countries may be operating at above planned safety levels. In short, asset owners need to make sure that they are operating and producing energy in the most responsible and sustainable way, while at the same they face growing pressure from stakeholders to take a more long-term view in their planning and decision-making, particularly when it comes to energy security, environmental and social responsibility.
Steel at the heart of energy production
Energy facilities both onshore and offshore are heavily dependent on steel as a construction material as any image of a modern refinery will highlight. In addition, there are pipelines for transporting oil and gas and distributing products. Coal fired power stations – which supply some 40% of world energy – also make extensive use of steel although it may be less visible. Steel is needed in cooling systems, heat exchangers, combustion chambers, boiler super-heaters, reheater tubes and water wall panels among others.
“Steel is an ideal material for the uses it is put to, but it does require proper management to function as intended. The owners and managers of energy assets clearly need to know all about their production process for safe and efficient operations. That said they should not lose sight of the behaviour of steel under challenging conditions. Steel components in operating facilities are challenged by things like extreme corrosion conditions, chemicals and operational temperatures and also by the effects of fires, and explosion dangers which can occur in even the best run facilities for numerous reasons,” says Ekaterina Mezhentseva, Global Solutions Manager, Jotun Performance Coatings.
Corrosion is an especially serious issue. Easily spotted on components that are visible to the eye but much of the steel in energy facilities is hidden by other materials insulating the steel against the effects of weather or heat. This can lead to a phenomenon known as Corrosion Under Insulation (CUI).
Growing concerns around the condition of energy facilities
Numerous studies by bodies such as the EU, OECD and DNV among others highlight concerns around corrosion issues. In the EU around 20% of major refinery accidents since 1984 indicate corrosion failure as an important contributing factor. A 2021 study by DNV for the Norwegian Petroleum Institute found that operators consider CUI as ‘the biggest threat to the mechanical integrity of oil and gas industry facilities.’ The consequences of CUI might be a serious fire or explosion but could also lead to release of chemicals or hydrocarbons into the environment affecting public health or environmental degradation.
And it is not only fossil fuel facilities that can be affected by severe corrosion. In 2022 it was reported that corrosion in pipework caused shutdowns on several nuclear reactors in France, leading to increased energy prices and questions of energy availability. Any shutdown will of course result in lost revenue but will also require other facilities to up production to fill the gaps placing more pressure on those facilities as well.
There is another side to this as well. Corroded or damaged steel will need to be replaced and that is an expensive exercise. But as well as the cost to the asset owner, there is an environmental and sustainability aspect as well.
Ekaterina Mezhentseva
Global Solutions Manager, Jotun Performance Coatings
There is another side to this as well. Corroded or damaged steel will need to be replaced and that is an expensive exercise. But as well as the cost to the asset owner, there is an environmental and sustainability aspect as well.
Ekaterina Mezhentseva
Global Solutions Manager, Jotun Performance Coatings
According to the World Steel Association, construction is one of the most important steel-using industries, accounting for over 50% of world steel demand. Furthermore, the IEA estimates that direct CO₂ emissions due to crude steel production is approximately 1.4 tonnes of CO₂ per tonne steel produced. Globally, the steel industry consumes 5.9 % of global energy and emits 6-9 % of global CO₂ emissions. Cutting the requirement for new steel by better protecting that in use will reduce that impact.
Maintaining steel integrity tackling areas of concern
“It is clear that there are three areas of concern that can arise from failure of steel components namely the unexpected interruptions and downtime, increased risk of accidents, and environmental impact. That is why Jotun is committed to support the energy sector in maintaining steel integrity so that asset owners can avail themselves of our long history of protecting steel,” says Ekaterina.
Jotun has close to a century of experience in developing products to protect and ensure the longevity of many materials but especially steel. Working with partners from a diverse range of industries Jotun has become an expert authority on coating performance. That has been achieved by understanding the problems and investing time and resources on developing, testing and improving coating performance in the lab and in field testing.
References:
Corrosion‐Related Accidents in Petroleum Refineries
Ptil - Maintenance management - corrosion under insulation (CUI)
Progressive corrosion and poor maintenance – half of France’s nuclear reactor fleet is offline
The carbon footprint of steel corrosion