Insights
Protecting offshore wind investment
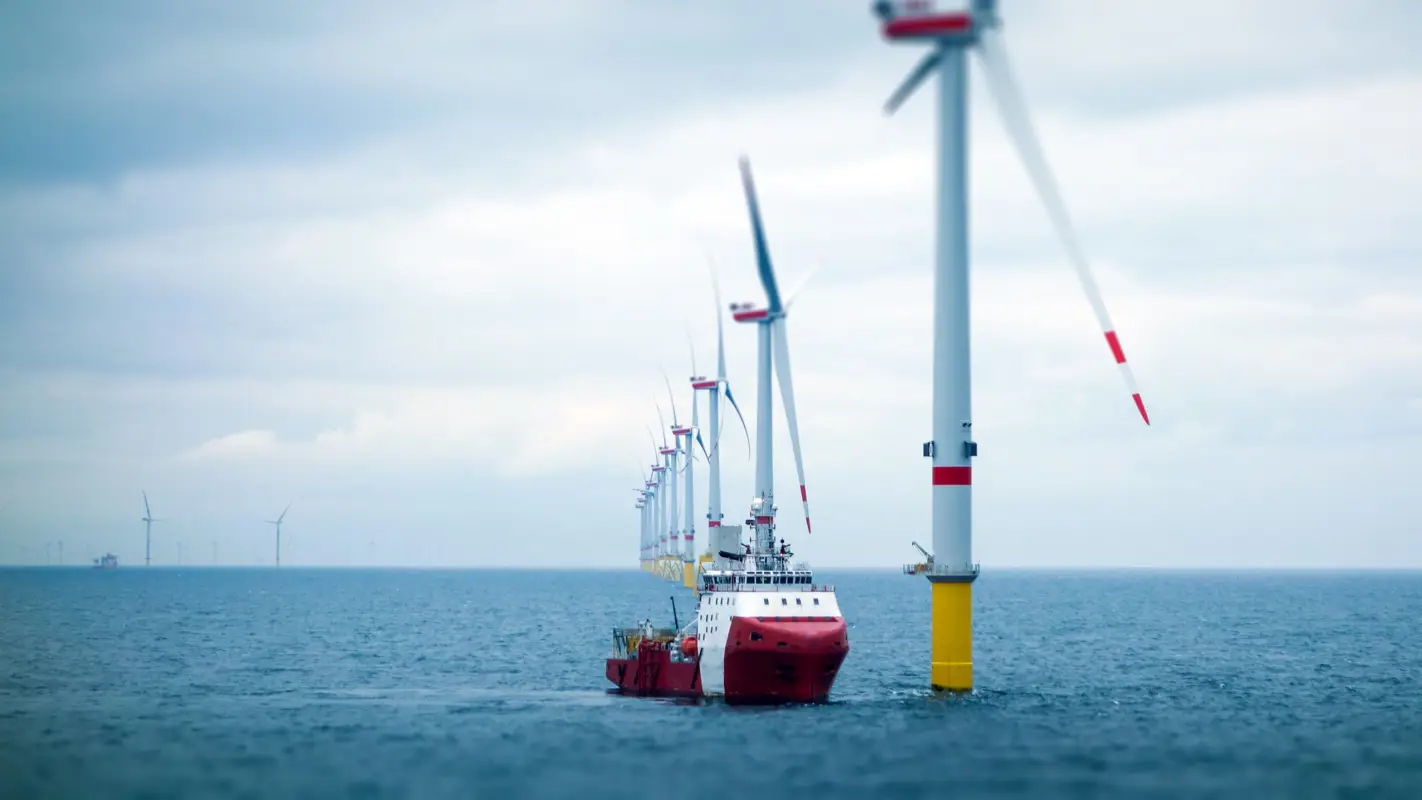
tháng 9 12, 2023
Tried and tested performance coatings can help offshore wind operators ensure asset longevity and sustainable operations.
Billions of dollars are being invested in a global booming offshore wind sector. The prize is intended to be energy security, a cleaner, greener method of energy production and eventually cheaper energy prices for consumers. However, energy will only be produced, and income generated so long as the turbines keep on turning. Therefore, protecting the physical assets and ensuring they operate at peak efficiency for the longest time possible should be a key consideration for operators and stakeholders, argue coating experts at Jotun.
According to the Global Wind Energy Council’s (GWEC) 2022 report on Offshore wind, 2021 saw 21.1GW offshore wind reach grid connection worldwide, three times more than in 2020, setting a new record in the offshore wind industry. The 21.1GW of new installations brought global cumulative offshore wind power capacity to 56GW, showing year-on-year growth of 58% and representing 7% of total global cumulative wind installations.
GWEC’s 2023 report covering both offshore and onshore wind illustrates the variable nature of new installations offshore with new offshore wind capacity commissioned in 2022 dropping to 8.8 GW. However, this still made 2022 the second highest year on record.
The same report details a new initiative to drive offshore wind installations. In September 2022, GWEC along with the Danish government and IRENA (International Renewable Energy Agency – a governmental organisation of 167 nation states and the EU) founded the Global Offshore Wind Alliance (GOWA). GOWA aims to contribute to achieving a total global offshore wind capacity of at least 380GW by 2030 and 2,000GW by 2050, with 35GW being deployed on average each year through the 2020s and a minimum of 70GW annually from 2030.
BloombergNEF’s Offshore Wind Forecast in February 2023, also highlights global offshore wind installations are on track to grow 10-fold by 2035, reaching 519 GW. Much of the new capacity will be in the mature markets of China, the UK, Germany and the Netherlands. Emerging markets like the US, Taiwan (Province of China), France, South Korea, Poland and Japan will make significant contributions, and Norway, India, Spain and Greece will install their first projects later in the decade. Post-2030, more new markets will contribute to build, including Colombia, Brazil and Sweden.
“Clearly, countries see the offshore wind sector as a key facilitator of their long-term climate goals, as they set new targets and increase existing ones,” says Christian Boge, GKA Manager - Power Generation, Jotun. “For sure the rate of annual increase in installed and planned new capacity is accelerating rapidly, but there are fluctuations in the instalment rate for a variety of reasons not least because it takes a long time for new projects to obtain permission, followed by an average two-year installation time.”
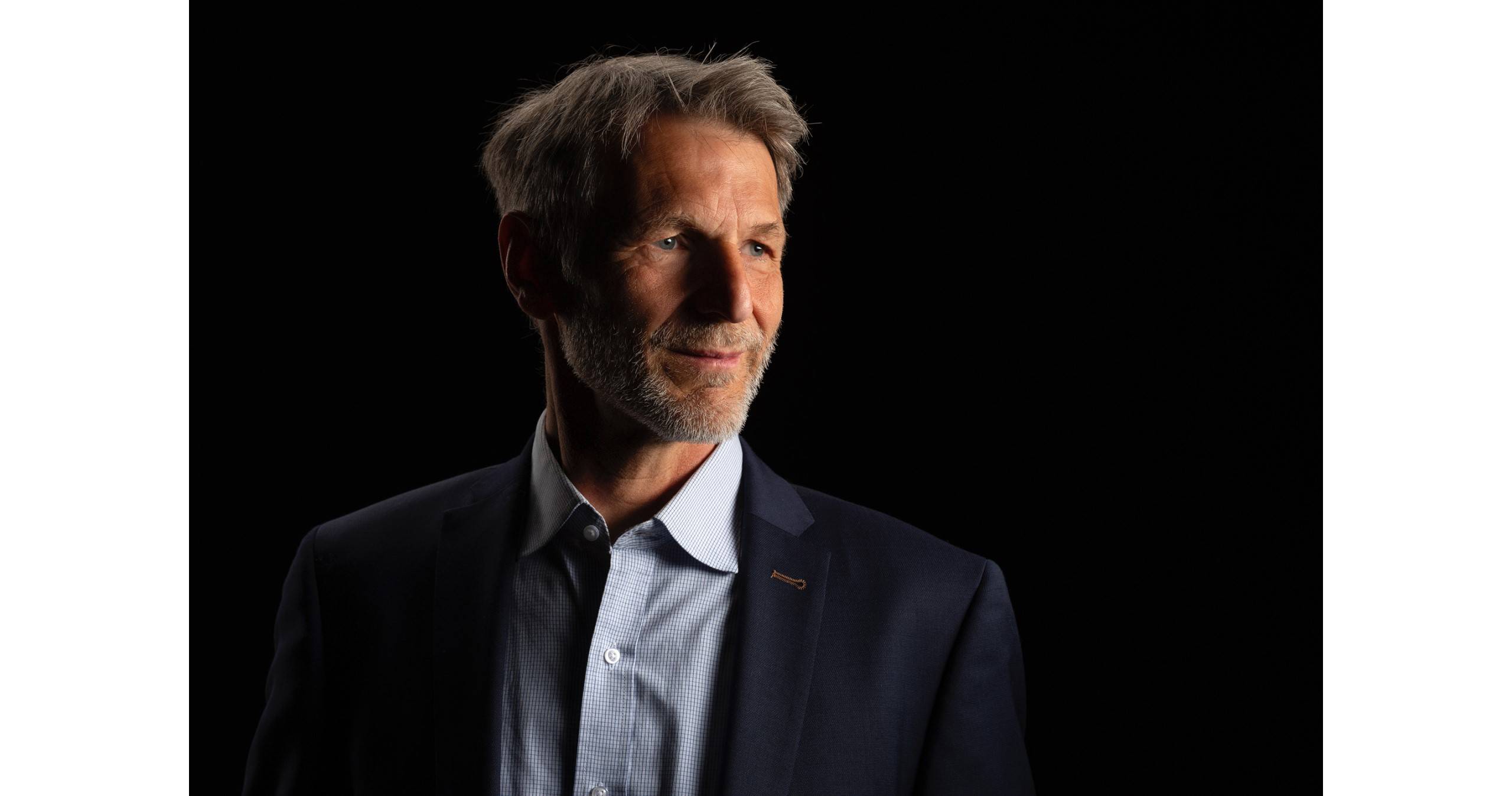
Increasing turbine sizes and costs
Currently, the majority of new turbines are 10MW types although 12MW and 14MW types are available. At 10MW, each GW of windfarm capacity requires 100 turbines falling to 72 at 14MW size. It follows that to meet the 35GW annual target set by GOWA, somewhere between 2,500 and 3,500 turbines will be needed annually through the 2020s rising to double that by 2030. Norwegian consultant Rystad Energy reports that total capital expenditure for offshore wind is projected to more than double from $46 billion in 2021 to $102 billion in 2030.
The final figures could in fact be higher since the first generation turbines with a lifespan of 20-25 years are now approaching end of life and will need to be replaced. That lifespan will in future need to be surpassed by the new generation of turbines especially as subsidies are now less generous and government support is being reduced in many countries.
Cutting maintenance costs
As well as reducing cost by increasing asset longevity, maintenance costs also need to be cut drastically. “These will vary from operator to operator and reliable industry averages are as yet hard to quantify. The rule of thumb is that offshore maintenance costs are between $800 and $1,000 per m2,” says Chris O’Rourke, GKA Manager – Offshore Energy, Jotun. “Physical maintenance of the whole structure is only part of the additional cost as there is also a need for more and larger ships to transport the maintenance workers and equipment.”
Chris explains maintenance and repairs to the rotational elements such as blades, gearboxes, and the generating equipment are hard to reduce so it is in developments such as recyclable blades that some savings can be made but it will be in the area of the substructures needed for the whole life of the asset where the major savings can be achieved. Given the harshness of the offshore environment it should not be a surprise that corrosion of the structure, particularly in the tidal and splash zones is the biggest threat.
“Maintenance of offshore structures is not easy and is dangerous for the maintenance teams sent out to do the work – often under extreme weather conditions. So, the adoption of suitable solutions, equipment and technology are also crucial to ensure long-term, profitable, safe operation of assets. This also includes the coating system that needs to be capable of providing corrosion protection for the assets design life,” adds Chris.
Most offshore wind turbines now operating are of the monopile type and are located in depths of up to 30m. As the size and capacity of turbines grow, they are planned to be located in depths of around 50m. “The monopile offshore turbines may look very different from offshore oil and gas structures, whereas the new floating offshore wind structures are more complex in design but do resemble oil and gas structures. Regardless, both types being made of the same materials are subject to the same problems as other offshore structures,” points out Scott Kim, Global New Building Solutions Manager, Jotun.
Proven protection performance
“When it comes to combating corrosion, there are various quality coatings capable of providing protection of the turbines and blades. However, when it comes to the foundation structures, which will be used for the whole life of the turbine, that’s not the case. And given the increasing emphasis on sustainable operations, it is not surprising that owners and operators are seeking longer lifespans to get the best returns on capital and operational expenses,” says Scott.
Jotun’s experience from the oil and gas sectors stretching back almost half a century shows that simple epoxy resin coatings are the least effective and glass fibre reinforced polyester (GFRP) coatings can provide very long-lasting protection with little maintenance. What maintenance is needed is generally due to impact damage to the coating caused by floating objects and contact by vessels.
Introduced during the 1970s, Baltoflake was one of the first performance coating products targeted for offshore environment deployment where strong corrosion resistance and excellent mechanical properties are required. The coating has glass flake materials incorporated into polyester to create a structure that is 5-20 times more impermeable than resin alone.
“Evidence of the protective properties of Baltoflake on offshore structures has been demonstrated by testing of sections of decommissioned structures from the oil and gas industries. DNV inspected sections of jacket from a North Sea oil platform which was installed in 1972 and decommissioned in 2020. Jotun’s Baltoflake coating was applied to the platform in the late 1980s and, despite over 30 years’ exposure to the North Sea’s harsh environment, analysis revealed that the coating at the splash zone was intact, still smooth and showing no signs of delamination. Furthermore, corrosion of the under- film material was shown to be absent,” adds Scott.
The coating on the sections had undergone zero to minimal maintenance since its application over 30 years previously and yet the tests showed the barrier properties of the coating system were still excellent, and it retained a similar mechanical performance to that of a newly prepared reference sample.

Making renewable energy last longer
Going beyond the cost benefit argument, Jotun’s coating experts emphasise the environmental benefit of applying a highly effective coating such as Baltoflake reinforces the fundamental use of offshore wind as an energy source. Indeed, the main driver of wind power is that is considered a clean and renewable energy source. As well as providing electric energy direct into grids, offshore wind also opens up the opportunity to scale the production of green hydrogen and power-to-X fuels, thereby aiding in the decarbonisation of energy intensive sectors.
And whilst the basic power of wind is genuinely free, there are environmental implications for the infrastructure needed to harvest that power. According to the International Energy Agency (IEA) steel production is energy intensive and around 1.85 tonnes of CO₂ is emitted for each tonne of steel made. Reducing the corrosion allowance of offshore turbines by just 1mm will save 50 tonnes of steel for the typical tower. For the expected 30,000 turbines needed by 2030 that equates to 1,500,000 tonnes of steel saved.
“As the purpose of offshore wind is to produce clean emission free energy then any action that reduces the need to repair or replace steel structures in the sector and which keeps assets operating efficiently is reinforcing that ambition,” opines Scott.
“The interest in longer maintenance-free lifespans of the offshore wind substructures should not come as a surprise. Baltoflake has a proven track record and removes the requirement for offshore wind developers to undertake expensive repairs or replacement due to corrosion. And by reducing overall maintenance costs and down time, we can help empower operators to focus their efforts on producing clean energy generation, effectively and safely,” adds Chris.
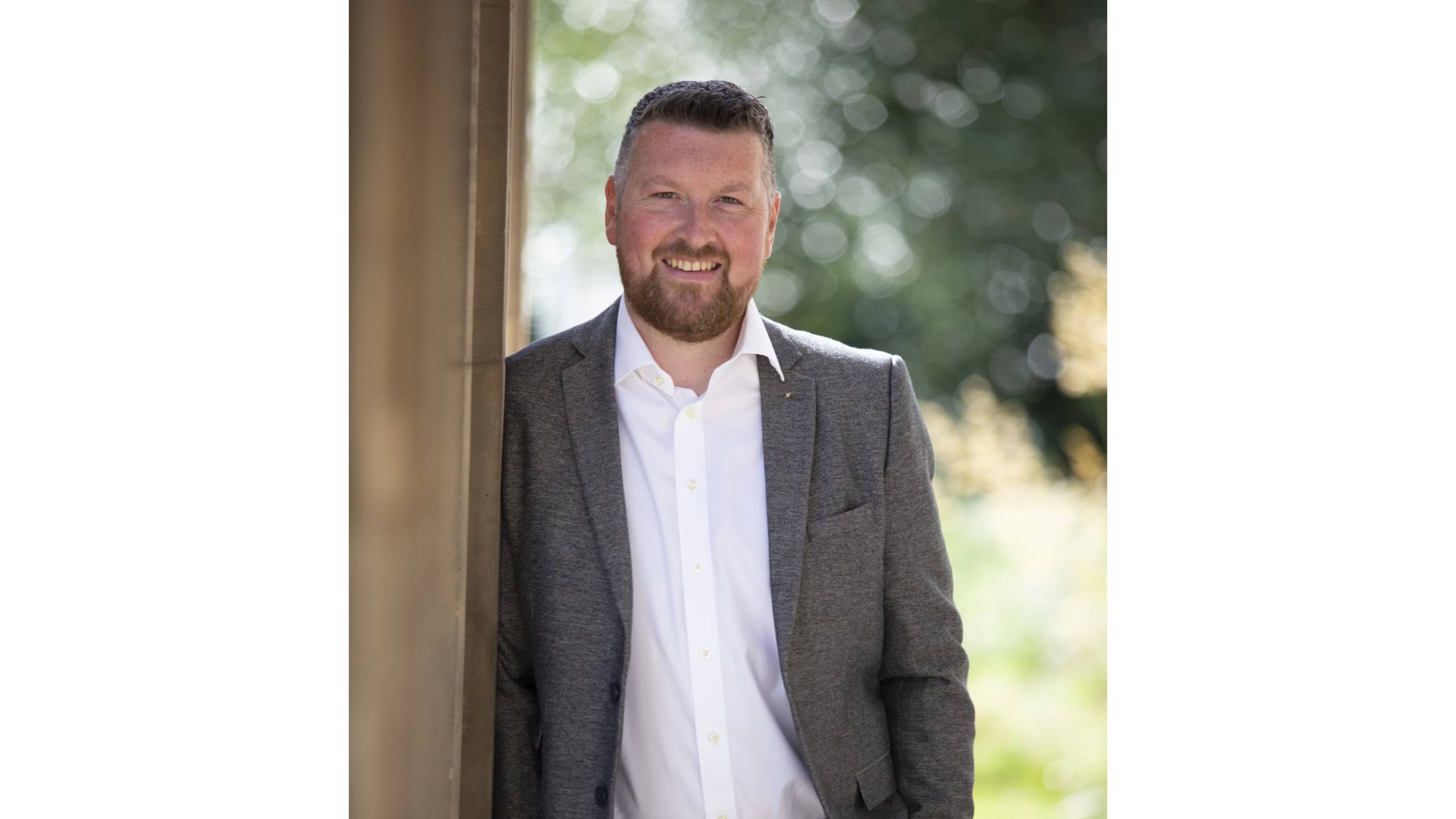
“Put simply, the point of wind power is to produce clean energy. This can only happen if the asset is performing as designed now and at the end of its lifetime. It takes a lot of energy to build the turbines and install it all. Why not use Baltoflake which has very low VOC emissions and is designed to protect and extend the life of expensive offshore wind assets?” argues Christian and concludes, “It’s as close to an apply and forget system as possible, cost and energy savings from not having to maintenance or steel replacement are huge.”